WesTech needed a product that could withstand the multiple flex cycles encountered during the hydrostatic pressure created within their innovative tertiary water treatment system. Learn more.
Innovators in high-durability flexibles
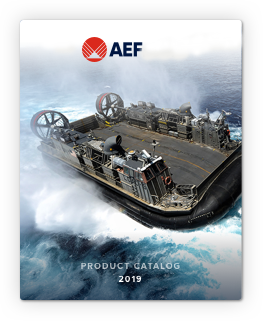
WesTech, a manufacturer of waste water treatment systems identified a need to develop an industrial separator diaphragm. WesTech needed a product that could withstand the multiple flex cycles encountered during the hydrostatic pressure created within their innovative tertiary water treatment system. They also needed a product that could withstand the long-term environmental exposures associated with this application. Previous attempts utilized a combination of commercially available technologies, including cold bond adhesives, but did not provide sufficient in-service performance to meet the life cycle requirements needed for this application.
While working with the customer to develop this application, AEF LLC implemented a cost effective, innovative, high-temperature vulcanizing solution to increase the life-cycle expectancy and longer-term resistance to environmental exposures during operation.
Resultant testing has shown that the materials selected and the vulcanization reduced the component’s flexural fatigue, increased diaphragm performance, and improved overall system effectiveness. Thanks to AEF’s cutting edge manufacturing processes and material selection for this application, AEF is now WesTech’s preferred supplier for their expanding tertiary water treatment business. This allows WesTech to continue to provide high quality, low cost, and custom fabrication product lines to their customers.
The Los Angeles Department of Water and Power (LADWP) needed a system for emergency preparedness efforts. The LADWP wanted their …